树脂基复合材料由于具有高比强、高比模、耐高温、耐腐蚀、耐疲劳、阻尼减震性好、破损安全性好、性能可设计等优点,已发展成为航空航天结构的基本材料。同时复合材料的先进性与其质量的离散性和高成本并存, 在实际应用中, 即使经过研究和试验制定了合理的工艺, 但在复合材料结构件的制造过程中还有可能产生缺陷, 引起质量问题, 甚至导致整个结构件的报废, 造成重大经济损失。因此复合材料的无损检测技术应运而生,早期复合材的无损检测技术主要沿用金属的无损检测,但发现其不能完全解决复合材料的无损检测问题,20世纪80年代后, 许多适应复合材料特点的无损检测新技术、新方法相继诞生。
首先我们来看一下树脂基复合材料常见缺陷有那些。
分层:基体,纤维,磨具热膨胀系数不匹配或存储时间过长;
夹杂:操作失误或预浸料本身有缺陷或操作不当;
脱粘:粘结剂选择不当或固化不完全;
孔隙:溶剂、低分子杂质的挥发,真空控制不当;
冲击、撞击损伤:工具脱落或其他外物体碰撞引起;
纤维曲屈:预浸料本身有缺陷或操作不当;
纤维断裂:预浸料中纤维质量不好。
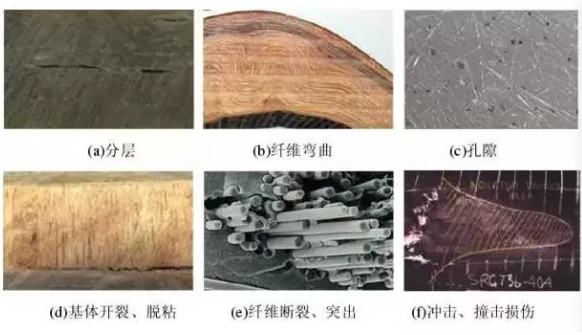
复合材料常见缺陷
这些缺陷都可以使用那些复合材料无损检测技术呢?
1、射线检测技术
射线检测技术( Radiographic Testing,即RT)是利用射线( X 射线、γ 射线、中子射线等)穿过物体时的吸收和散射的特性,检测其内部结构不连续性的技术。
适合于:孔隙、夹杂等体积型缺陷检测,对平行于射线穿透方向的裂纹有比较好的检测效果,对复合材料中特有的树脂聚集与纤维聚集等缺陷也有一定的检测能力,在铺层数量较少时,还可发现铺层内纤维弯曲等缺陷。由于分层缺陷对射线穿透方向上介质并无明显影响,因此分层缺陷在成像上并不明显。同样的原因,射线检测技术对平行于材料表面的裂纹也不敏感。
射线检测技术又分为如下三个类别:
射线照相
在所有的射线检测技术中,胶片射线照相技术发展最早,而数字式射线实时成像检测技术则发展最快。与胶片照相技术相比,数字式射线成像技术的成像质量与胶片照相技术相当,在检测的实时性、效率、经济性和易用性等方面则有着无可比拟的优越性,因而得到了快速的发展。目前,具备一定智能识别能力的实时成像检测技术已经应用于复合材料产品的在线检测,可对装配线上的工件进行实时快速检测,成为确保产品合格率的重要检测手段。
工业CT
层析摄影也叫计算机断层扫描成像( ComputedTomography,即CT) ,该技术是利用X 射线探测物体的内部,通过测定射线的衰减系数,采用数学方法,经计算机处理,求解出衰减系数值在某剖面上的二维分布矩阵,转变为图像画面上的灰度分布,从而实现建立断面图像的成像技术。通过分析断层面内密度的分布,就可以获得复合材料内部密度均匀性、微孔隙体积含量与分布等方面的信息。一般来说,CT 照片的对比度比X 射线照片的对比度要低,但因消除了不同层面图像叠加重影问题,实际可读性强于X 射线照片。不过CT 成像原理决定了密度高的物质会在一定程度上被放大,这也就导致了分层、孔隙、裂纹等损伤图像的尺寸比实际尺寸略小而纤维堆积等密度高的缺陷图像比实际尺寸略大的特有现象。
总的来说,CT 扫描成像的技术具有以下特点:
高空间分辨率和密度分辨率( 通常<0. 5%)
高动态检测范围( 从空气到复合材料再到金属材料) ;
成像尺寸精度高;
在穿透能量足够的情况下,不受试件几何结构限制。
局限性表现为: 检测效率低、检测成本高、双侧透射成像、不适合于平面薄板构件的检测以及大型构件的现场检测。利用CT 成像技术可以有效检测先进复合材料中的孔隙、夹杂、裂纹等缺陷,也可以测量材料内部的密度分布情况,如材料均匀性、微孔隙含量等。在工业应用上,美国在上世纪八十年代就研制出了用于检测大型固体火箭发动机复合材料壳体的工业CT 设备,并逐渐将该技术应用于其它复合材料结构的无损检测中,我国也于上世纪90 年代后期成功地将工业CT 技术应用于C /C 复合材料、碳/酚醛复合材料等的检测,解决了一些关键性的无损检测技术难题,取得了较好的经济效益与社会效益。
康普顿背散射成像检测技术
康普顿背散射成像( CST ) 技术是一种新的射线检测技术,它具有单侧非接触、检测灵敏度高、快速三维成像的特点,对低密度材料的检测可获得比透射成像更高的图像对比度,非常适合于复合材料等原子序数较低材料的物体。当被检物体结构复杂,或无法进行双侧成像检测时,CST 技术就显示出了独特的优势。目前,CST 技术在国外航空航天领域已经得到了广泛的应用,在国内,尚处于探索性研究阶段。
2、超声检测技术
超声波是指频率大于20kHz 的声波, 其波长与材料内部缺陷的尺寸相匹配。根据超声波在材料内部缺陷区域和正常区域的反射、衰减与共振的差异来确定缺陷的位置与大小。超声波检测主要分为脉冲反射法、穿透法等, 根据不同的缺陷来选择合适的检测方法。
适用于:超声波不仅能检测复合材料构件中的分层、孔隙、裂纹和夹杂物等, 而且在判断材料的疏密、密度、纤维取向、曲屈、弹性模量、厚度等特性和几何形状等方面的变化也有一定作用。
对于一般小而薄、结构简单的平面层压板及曲率不大的构件, 宜采用直接接触脉冲反射法;
对于小或稍厚的复杂结构件, 无法采用直接接触脉冲反射法时, 可采用水浸或喷水脉冲反射法和接触延迟块脉冲反射法;
对于大型结构和生产型的复合材料构件的检测宜采用喷水穿透法或喷水脉冲反射法。由于复合材料组织结构具有明显的各向异性, 而且性能的离散性较大, 因而, 产生缺陷的机理复杂且变化多样, 再加上复合材料构件的声衰减大, 由此引起的噪声与缺陷反射信号的信噪比低,不易分辨,检测时应选合适的方法。
具体应用:飞行器零件等大型复合材料构件,蜂窝泡沫夹心等复杂结构件,曲面构件,波音飞机复合材料机身层合板结构的无损检测。
超声检测方法分为传统的超声波检测方法,超声导波检测方法,空气耦合超声检测技术,激光超声检测技术,相控阵超声检测技术。
3、红外热波检测技术
红外热波无损检测 ( Thermal Wave Testing)利用主动加热技术,通过红外热成像系统自动记录试件表面缺陷和基体材料由于不同热特性引起的温度差异,进而判定被测物表面及内部的损伤。
适用于:该检测方法特别适合于检测复合材料薄板与金属粘接结构中的脱粘、分层类面积型缺陷,尤其是当零件或组件不能浸入水中进行超声C-扫描检测以及零件表面形状使得超声检测实施比较困难时也可使用红外热波检测方法,红外热波方法能够准确确定复合材料中分层的深度,而且该方法具有非接触、实时、高效、直观的特点。
4、声-超声检测技术
声-超声( Acoustic-Ultrasonic)技术又称应力波因子( SWF) 技术。
适用于:AU 技术主要用于检测和研究材料中分布的细微缺陷群及其对结构力学性能( 强度或刚度等) 的整体影响,属于材料的完整性评估技术。采用声-超声振幅C 扫描技术也能够对复合材料与金属材料间的粘接界面进行有效检测,而且克服了超声反射技术信号清晰度不高、超声透射技术传感器可达性差的缺点。
5、声发射检测技术
声发射检测技术( Acoustic Emission) 是通过对复合材料或结构在加载过程中产生的声发射信号进行检测和分析,对复合材料构件的整体质量水平进行评价的一种检测技术。
适用于:反映复合材料中损伤的发展与破坏模式,预测构件的最终承载强度,并能够确定出构件质量的薄弱区域。声发射技术是检测复合材料结构整体质量水平的非常实用的技术手段,使用简单方便,可以在测试材料力学性能的同时获取材料动态变形损伤过程中的宝贵信息。
6、涡流检测技术
涡流检测技术( Eddy Current Testing) 是利用导电材料的电磁感应现象,通过测量感应量的变化进行无损检测的方法。
适用于:用于导电材料,可以用于碳-碳复合材料与金属基复合材料的检测。由于端头效应的存在,该方法在边界处的检测效果不好,同时该技术需要用标准试样进行对比,因此其应用受到了限制。
7、微波检测技术
微波是指频率为300MHz ~3000GHz 的电磁波,是无线电波中一个有限频带的简称,是分米波、厘米波、毫米波和亚毫米波的统称。微波频率比一般的无线电波频率高,通常也称为“超高频电磁波”。
适用于:微波指向性高,在复合材料中穿透能力强、衰减小,适合于检测厚度较大的材料。对结构中的孔隙、疏松、基体开裂、分层和脱粘等缺陷具有较高的灵敏性。上世纪60 年代,微波检测技术就已经用于大型导弹固体发动机玻璃钢壳体中的缺陷和内部质量的检测。实践证明,利用反射法测量的厚度误差小于0. 125mm,利用穿透法可测定0. 02mg /cm3 的密度变化。由于微波探伤技术不能穿透导体,因此这种检测方法很难应用于整机检测。
8、流体渗透法
流体渗透检测法仅仅适用于具有开放性伤口的缺陷或损伤,这种方法是采用特制的渗透剂对缺陷和损伤进行染色,但是染色过程中会污染材料,在一定程度上会增加修补难度,目前使用较少。
9、激光全息法
激光全息检验法( Laser Holography) 是激光全息照相和干涉计量技术的综合运用。这种技术的依据是物体内部缺陷在外力作用下,使它所对应的物体表面产生与其周围不相同的微量位移差。然后用激光全息照相的方法进行比较,从而检验出物体内部的缺陷。这种检验方法由于设备昂贵、需要冲洗显影、对环境振动敏感和需要对被测物加载,因此限制了推广能力,目前主要在实验室使用。
10、目测法
就是人眼观察复合材料表面的肉眼可见的缺陷,主要是表面的裂纹和损伤,优势在于成本低,效率高,但是具有较大人为因素。