由残余应力引起结构件疲劳、开裂,从而诱发的航天事故不在少数,比如2002年5月的华航空难,原因就是飞机尾部的裂纹在应力腐蚀作用下的快速扩展。
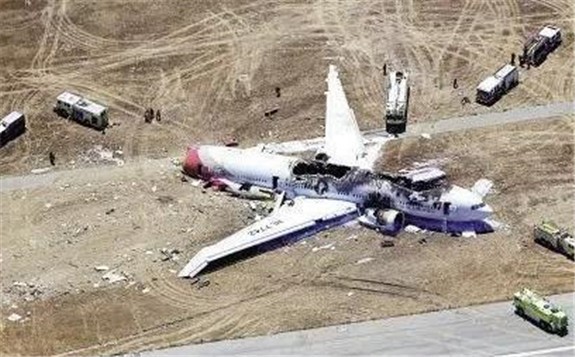
残余应力在航空领域的影响不容小觑
航空制造业尤其要特别重视残余应力,这是因为其在材料、结构和工艺等方面具有鲜明的行业特征。
材料方面,除各种钢、铝合金等传统材料仍占有一定比列外,钛合金、高温合金等高性能、难加工材料所占比例逐渐增大;
结构方面,由于高性能、轻量化和高可靠性的设计要求,采用整体结构和复杂型面结构的零件比例大大增加,因此零件几何尺寸大、型面复杂、工艺特征多、壁厚小; 同时,金属材料毛坯仍由铸造、锻造、预拉伸、轧制等多种工艺制成,毛坯的初始残余应力大,切削加工过程中呈现出加工精度要求高、切削加工过程材料去除量大、加工变形控制难度大等特点; 此外,油箱与液压系统的应力腐蚀问题,结构件的疲劳寿命问题等直接影响着飞行器的使用安全。因此,残余应力已经成为影响加工质量、变形控制、加工效率与飞行器安全的重要因素。
残余应力的检测的重要性
至今,工件中残余应力的产生、测量、控制和调整以及它们对各工程项目的影响规律等方面仍有许多问题没有解决,相关的研究成果仍不能定量地满足工程设计的需要。不过研究人员发现,残余应力是加工变形的根源,如果能进一步有效降低或均化加工毛坯或工件的残余应力水平,必将大大降低工件的变形潜能,控制加工变形,提高加工质量。因此,对残余应力进行正确检测与合理分析,为工程人员解决变形开裂问题提供了关键性的残余应力量化依据。
残余应力检测技术及其特点
现有的残余应力测量方法主要包括有损检测(机械法)与无损检测(物理法)两大类:前者对试件具有一定破坏性,通过应力释放的方式可以测得第一类残余应力,主要包括盲孔法、剥层法、取条法、切槽法等;后者为非破坏性的检测方式,包括激光干涉法、云纹分析法、X射线衍射法、中子衍射法、磁应力法和超声法等。
X射线法同时检测影响宏观尺寸变化的第一、二类残余应力,具有原理成熟(通过测量晶格间距变化求出应力大小)、方法完善、可重复测量、测试精度高、无损等优点,且可以现场操作并绘制应力云图,为目前先进、无损、可靠,切实可行的残余应力测定方法,在残余应力无损检测领域具有公认的权威性,有助于进行工艺实施前后的效果验证:
1、由于X射线透射深度较浅,不改变材料状态,属于无损测量。即以无接触的方式测量试件上的应力,尤其在研究各种表面强化技术的机理,评价各种加工手段对应力状态的影响情况,检验其工艺效果,以及控制表面机加工质量等方面具有实际意义;
2、通过与其它材料剥离、电解抛光方法配合,可实现对残余应力的逐层测定,适用于精确测定应力沿层深的分布;
3、通过多点多向测量,可绘制工件应力分布的完整云图;
4、应力测量值指导并修正CAE的应力仿真值,可以相对准确、全面的掌握工件在各个加工环节的应力状态,并引申得到加工变形情况。